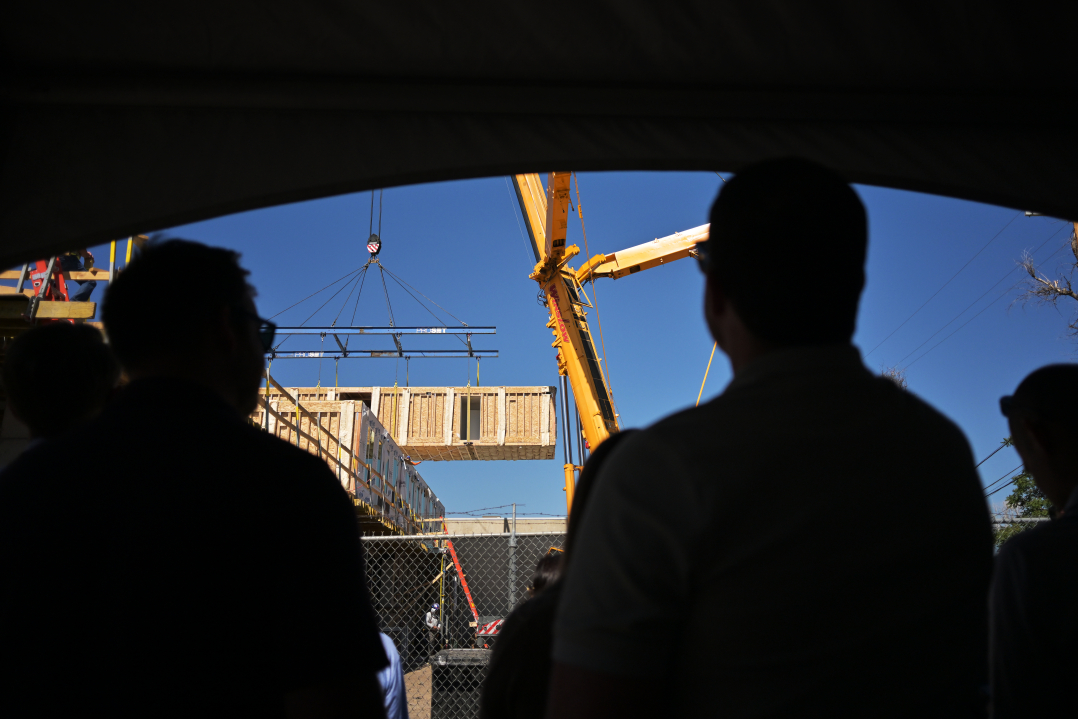
Under the shade of a tent, people watch as a modular unit, part of a total of a 77-unit apartment building, is hoisted into place via a crane at West Holden Place construction site in Denver on July 10, 2024. (RJ Sangosti/The Denver Post)
On a sunny Wednesday morning, a loud horn sounds before a large crane hoists a 25-ton box skyward in Denver’s Sun Valley neighborhood. It then swings it into position and as gently as possible, places it on the third floor of what will soon be a six-story apartment building.
The box has windows, insulation, painted drywall, flooring, plumbing and electrical wiring, almost everything needed. Even the appliances are pre-installed, including water heaters, toilets and kitchen sinks. After the boxes are placed, a crew will connect the plumbing and utilities through the corridors, finishing those and eventually the exterior.
“We hope to do a lot more of these,” Adam Berger with Adam Berger Development told the crowd gathered to see modules put into place on West Holden Place, a 77-unit mixed-income development.
Using a modular approach costs 20 percent to 25 percent less than traditional methods and shaves at least 40 percent off of construction times, Berger said.
Those savings, when combined with affordable housing funds from Denver, the Colorado Housing and Finance Authority and the Colorado Division of Housing, will be enough to make rents on most of the units affordable to middle-income renters earning between 80 percent and 120 percent of Denver’s median income.
Although affordable housing has historically focused on building for those earning 60 percent of area incomes, the problem has reached crisis levels even among people in middle-income ranges, said Cris White, CEO of CHFA.
Market rents on one-bedroom units at West Holden Place are expected to start at $1,900, with affordable rents, still to be determined, below that for qualified tenants. Pre-leasing is expected to begin next month.
In 2015, Berger started building modular townhomes, duplexes and triplexes, taking on larger and larger projects. He describes West Holden Place as Denver’s largest modular apartment building so far, and a test case to prove modular techniques can work at scale in providing improved affordability.
Although the bulk of West Holden Place will come together in a week, Berger and his team have spent three years designing and engineering the project, sourcing a manufacturer after the first effort failed and devising a financial model that balances affordability with market returns.
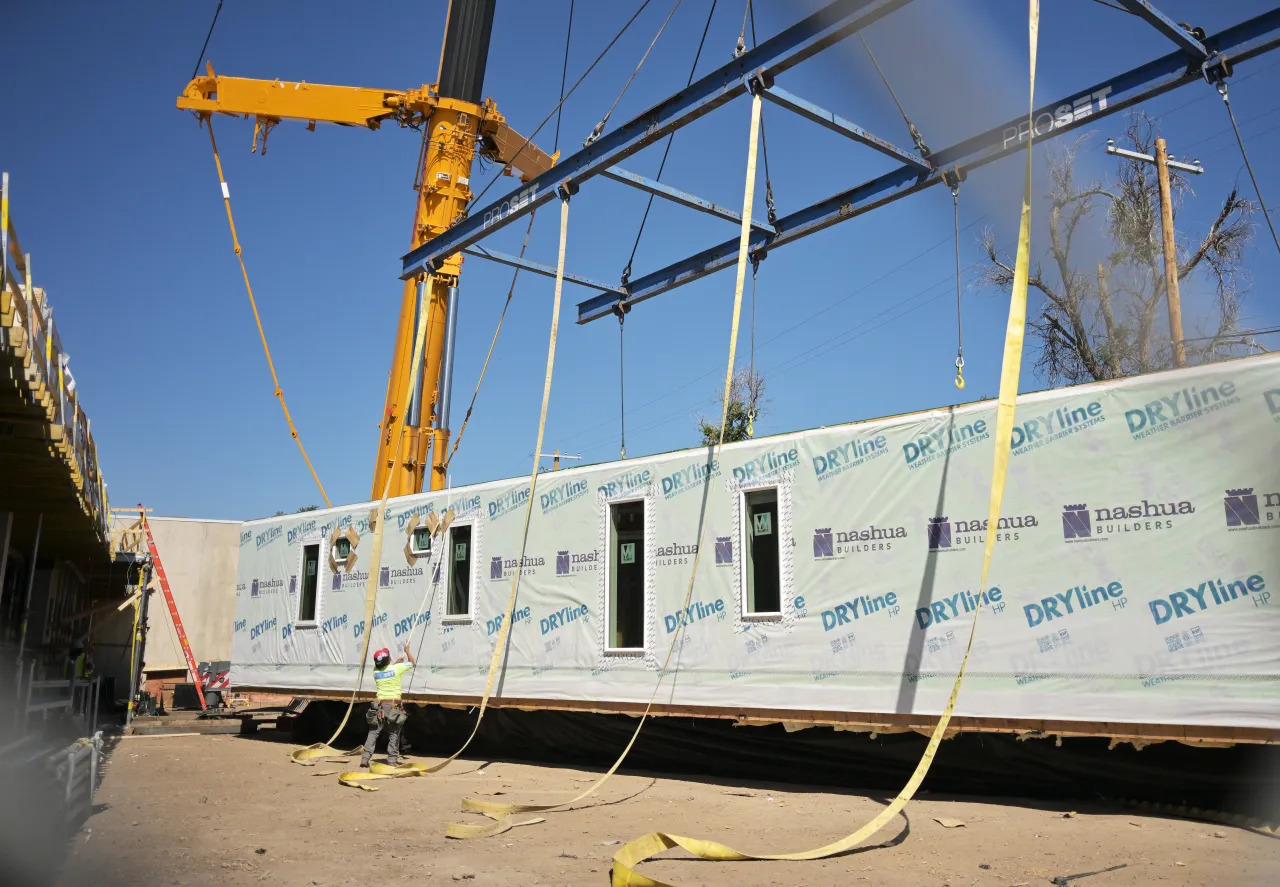
Crews work to move a modular unit, part of a 77-unit apartment building, into place via a crane at West Holden Place construction site in Denver on July 10, 2024. (RJ Sangosti/The Denver Post)
Although faster and cheaper is an important goal, it isn’t the end-all. Berger wants to build apartments at a high construction standard and with the quality finishes needed to compete with new market-rate units. He said his apartments are energy efficient, electric only, per new requirements, and have much better soundproofing than the competition.
With the design established and the funding model set, he hopes it will be a case of rinse and repeat, allowing future projects to come forward at lower costs and faster completion times as his crews gain more experience.
Next up is a modular apartment building in Englewood, near Swedish Medical Center and Craig Hospital, in an area that is rapidly getting denser. The new units, however, are mostly not affordable to lower-wage medical workers, which Berger hopes to change.
After that is a project in Olde Town Arvada and negotiations are underway for two parcels in the River North Neighborhood.
Modular multifamily homes, including hotels and assisted living facilities, represents an expanding segment in a market slowing under the pressure of higher interest rates.
“We will set 3,000 units this year, including 60 modules at this site,” said Matt Mitchell, owner of ProSet Setting Service in Telluride, the company putting the building together.
ProSet is expected to average around nine modules a day with its crew of 18, but could do up to 15 a day. Denver, to avoid worsening rush hour congestion, limits when ProSet trucks can haul the bulky modules from a storage lot in Centennial.
If the units had been stored on nearby lots, and Berger tried, the core of the apartment building could have gone up in four days. That contrasts with multiple months of crews rotating in and out of a traditional construction site and potentially disturbing neighbors.
One reason time frames are compressed with modular is that multiple activities can happen at the same time, said Jon Moon, head of business development at Nashua Builders in Boise, Idaho.
While Berger and his team were laying the foundation and getting the platform ready, Nashua workers assembled the modules in a controlled environment, allowing for better quality control and lower waste.
“While they were pouring concrete, we were building boxes,” Moon said. Each unit made its way through 30 work stations and took about 2.5 weeks to build.
Berger said he initially tried to source the modules locally, through IndieDwell, which opened up a factory in Pueblo in 2020 to construct steel frame boxes. But IndieDwell ran into financial troubles, couldn’t honor its contracts and now faces a state investigation over whether it defrauded taxpayers.
To avoid further delays, Berger turned to Nashua Builders, an established firm founded in 1961.
Colorado once had a respectable and rising modular construction industry before the housing crash and Great Recession wiped out most of the players, including a firm he had started, Mitchell said. He pivoted and in 2014 began focusing on helping developers install the modules.
About seven years ago, Mitchell said he worked with only a couple of module manufacturers. Now he counts about two dozen manufacturers whose modules he sets all across the West.
The key for Berger is getting the returns high enough to attract private investors, generating enough cash flow to make his lender, in this case First Western Trust Bank, confident of repayment, and winning support from CHFA and Colorado Division of Housing to cover the gap.
At the center of all of that is getting costs low enough to make the financial model work, and that is where modular construction, with its greater efficiency, proves a game changer, Berger said.
Berger bypassed using federal LITEC credits, which are limited in amount and highly fought over. They also target affordability at 60 percent of area median incomes. As rents and home prices have risen in Colorado, even households making a typical income can’t afford what the market is providing.
Zillow estimates that the mid-point home sold in Denver would require twice the median household income. And while renting remains a more affordable option, rents on the new luxury apartment units that now dominate the market don’t align with typical incomes.
Things are so tight in metro Denver that about 70,000 non-related households are doubled up and would likely get their own places if they could afford to, according to Zillow.
Denver’s loosening of parking requirements has also helped make the project viable. There will be 0.75 parking spaces per unit, which is sparse compared to older projects. But it should work with a light rail station a block away and the Front Range bike path close by, Berger said.
Although he has other apartment projects on the drawing board, Berger said his bigger vision is to build for governments, nonprofits and even employers seeking to address the shortage of affordable housing, which is increasingly becoming a middle-class problem.
“We don’t need to own everything. We will build it for you,” he said.
This story was originally published by The Denver Post, a BusinessDen news partner.
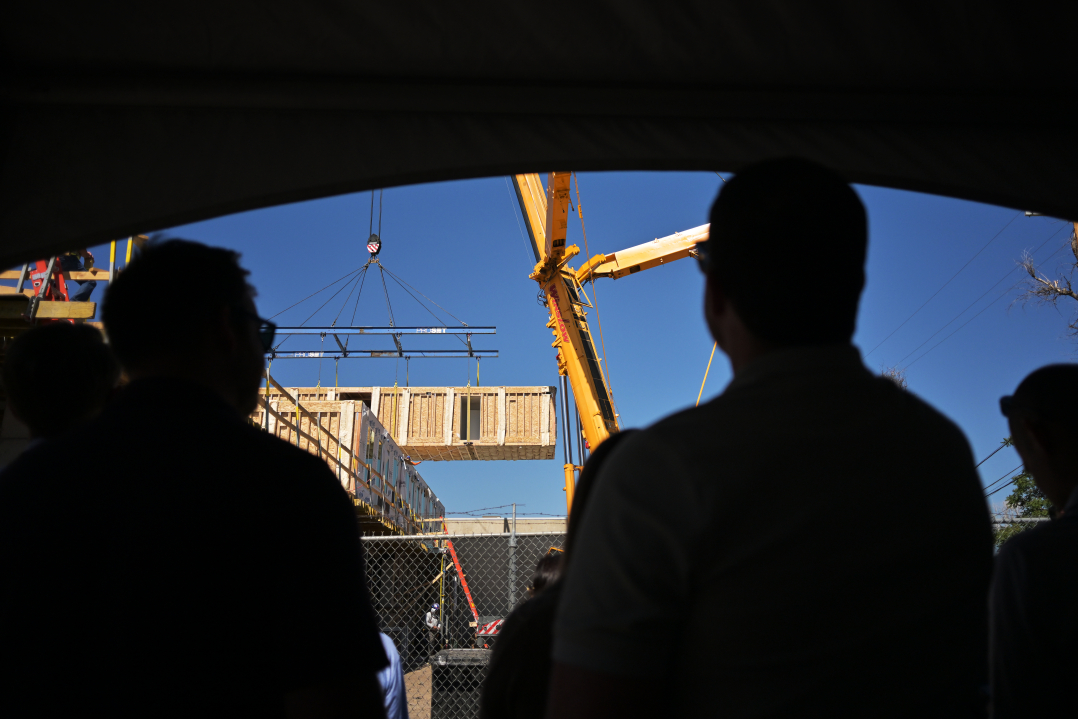
Under the shade of a tent, people watch as a modular unit, part of a total of a 77-unit apartment building, is hoisted into place via a crane at West Holden Place construction site in Denver on July 10, 2024. (RJ Sangosti/The Denver Post)
On a sunny Wednesday morning, a loud horn sounds before a large crane hoists a 25-ton box skyward in Denver’s Sun Valley neighborhood. It then swings it into position and as gently as possible, places it on the third floor of what will soon be a six-story apartment building.
The box has windows, insulation, painted drywall, flooring, plumbing and electrical wiring, almost everything needed. Even the appliances are pre-installed, including water heaters, toilets and kitchen sinks. After the boxes are placed, a crew will connect the plumbing and utilities through the corridors, finishing those and eventually the exterior.
“We hope to do a lot more of these,” Adam Berger with Adam Berger Development told the crowd gathered to see modules put into place on West Holden Place, a 77-unit mixed-income development.
Using a modular approach costs 20 percent to 25 percent less than traditional methods and shaves at least 40 percent off of construction times, Berger said.
Those savings, when combined with affordable housing funds from Denver, the Colorado Housing and Finance Authority and the Colorado Division of Housing, will be enough to make rents on most of the units affordable to middle-income renters earning between 80 percent and 120 percent of Denver’s median income.
Although affordable housing has historically focused on building for those earning 60 percent of area incomes, the problem has reached crisis levels even among people in middle-income ranges, said Cris White, CEO of CHFA.
Market rents on one-bedroom units at West Holden Place are expected to start at $1,900, with affordable rents, still to be determined, below that for qualified tenants. Pre-leasing is expected to begin next month.
In 2015, Berger started building modular townhomes, duplexes and triplexes, taking on larger and larger projects. He describes West Holden Place as Denver’s largest modular apartment building so far, and a test case to prove modular techniques can work at scale in providing improved affordability.
Although the bulk of West Holden Place will come together in a week, Berger and his team have spent three years designing and engineering the project, sourcing a manufacturer after the first effort failed and devising a financial model that balances affordability with market returns.
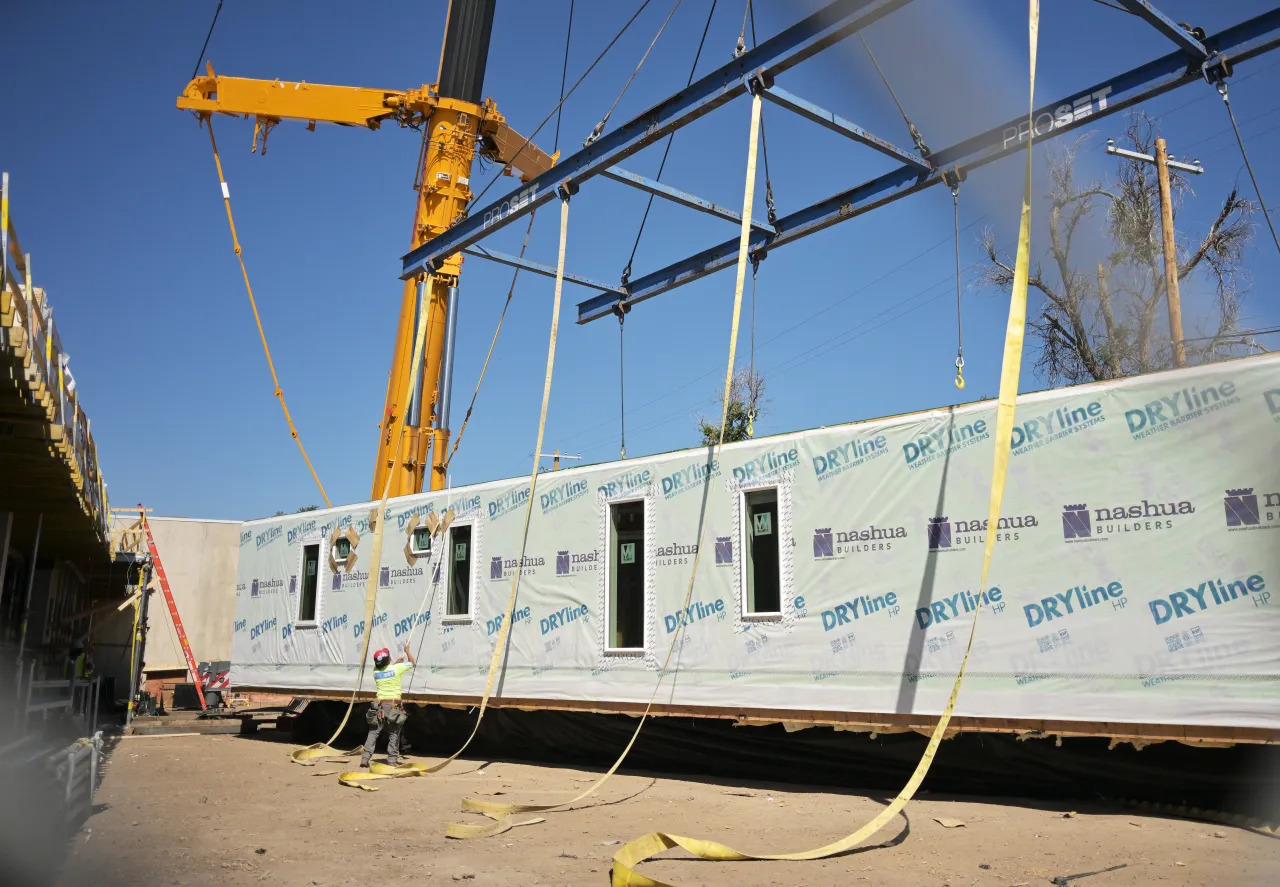
Crews work to move a modular unit, part of a 77-unit apartment building, into place via a crane at West Holden Place construction site in Denver on July 10, 2024. (RJ Sangosti/The Denver Post)
Although faster and cheaper is an important goal, it isn’t the end-all. Berger wants to build apartments at a high construction standard and with the quality finishes needed to compete with new market-rate units. He said his apartments are energy efficient, electric only, per new requirements, and have much better soundproofing than the competition.
With the design established and the funding model set, he hopes it will be a case of rinse and repeat, allowing future projects to come forward at lower costs and faster completion times as his crews gain more experience.
Next up is a modular apartment building in Englewood, near Swedish Medical Center and Craig Hospital, in an area that is rapidly getting denser. The new units, however, are mostly not affordable to lower-wage medical workers, which Berger hopes to change.
After that is a project in Olde Town Arvada and negotiations are underway for two parcels in the River North Neighborhood.
Modular multifamily homes, including hotels and assisted living facilities, represents an expanding segment in a market slowing under the pressure of higher interest rates.
“We will set 3,000 units this year, including 60 modules at this site,” said Matt Mitchell, owner of ProSet Setting Service in Telluride, the company putting the building together.
ProSet is expected to average around nine modules a day with its crew of 18, but could do up to 15 a day. Denver, to avoid worsening rush hour congestion, limits when ProSet trucks can haul the bulky modules from a storage lot in Centennial.
If the units had been stored on nearby lots, and Berger tried, the core of the apartment building could have gone up in four days. That contrasts with multiple months of crews rotating in and out of a traditional construction site and potentially disturbing neighbors.
One reason time frames are compressed with modular is that multiple activities can happen at the same time, said Jon Moon, head of business development at Nashua Builders in Boise, Idaho.
While Berger and his team were laying the foundation and getting the platform ready, Nashua workers assembled the modules in a controlled environment, allowing for better quality control and lower waste.
“While they were pouring concrete, we were building boxes,” Moon said. Each unit made its way through 30 work stations and took about 2.5 weeks to build.
Berger said he initially tried to source the modules locally, through IndieDwell, which opened up a factory in Pueblo in 2020 to construct steel frame boxes. But IndieDwell ran into financial troubles, couldn’t honor its contracts and now faces a state investigation over whether it defrauded taxpayers.
To avoid further delays, Berger turned to Nashua Builders, an established firm founded in 1961.
Colorado once had a respectable and rising modular construction industry before the housing crash and Great Recession wiped out most of the players, including a firm he had started, Mitchell said. He pivoted and in 2014 began focusing on helping developers install the modules.
About seven years ago, Mitchell said he worked with only a couple of module manufacturers. Now he counts about two dozen manufacturers whose modules he sets all across the West.
The key for Berger is getting the returns high enough to attract private investors, generating enough cash flow to make his lender, in this case First Western Trust Bank, confident of repayment, and winning support from CHFA and Colorado Division of Housing to cover the gap.
At the center of all of that is getting costs low enough to make the financial model work, and that is where modular construction, with its greater efficiency, proves a game changer, Berger said.
Berger bypassed using federal LITEC credits, which are limited in amount and highly fought over. They also target affordability at 60 percent of area median incomes. As rents and home prices have risen in Colorado, even households making a typical income can’t afford what the market is providing.
Zillow estimates that the mid-point home sold in Denver would require twice the median household income. And while renting remains a more affordable option, rents on the new luxury apartment units that now dominate the market don’t align with typical incomes.
Things are so tight in metro Denver that about 70,000 non-related households are doubled up and would likely get their own places if they could afford to, according to Zillow.
Denver’s loosening of parking requirements has also helped make the project viable. There will be 0.75 parking spaces per unit, which is sparse compared to older projects. But it should work with a light rail station a block away and the Front Range bike path close by, Berger said.
Although he has other apartment projects on the drawing board, Berger said his bigger vision is to build for governments, nonprofits and even employers seeking to address the shortage of affordable housing, which is increasingly becoming a middle-class problem.
“We don’t need to own everything. We will build it for you,” he said.
This story was originally published by The Denver Post, a BusinessDen news partner.